Consarc Corporation
Specialists in vacuum technologies
Business View Magazine interviews Michael Lister, Director of Business Development for Consarc Corp. as part of our focus on the melting and casting sector.
Consarc Corporation may have been around since 1962, but its dedication to engineering innovations has made it today’s leader in advanced vacuum technologies. “Our founder, Henry Rowan, a graduate of MIT, electrical engineer, industrialist, philanthropist, and entrepreneur wove his dedication to technological advancements throughout generations of Consarc employees – and we’re still constantly looking to develop groundbreaking technologies that will help our customers operate faster, safer, and more efficiently,” says Michael Lister, Consarc’s Director of Business Development. “As Henry Rowan said, ‘I hadn’t gone into business to do things the way everyone else did them. I wanted to do them better. Every job, every concept and detail represented the challenge to do something that had never been done before.’”
In fact, Consarc isn’t the only company operating under Henry Rowan’s corporate principles, as it is a member of the Inductotherm Group, a worldwide collection of manufacturers of advanced technologies, products, and systems for the induction heating and transformation of metals, specialty alloys, and engineered materials.
Consarc manufactures vacuum and controlled atmosphere melting and casting equipment for industries such as aerospace, power generation, automotive, and biomedical. These industries use Consarc furnaces to refine alloys and cast parts – superalloys for aeroengine and industrial gas turbine blades, vanes and discs; specialty steels for aircraft structures and landing gear; and titanium for aircraft structures, aeroengines, sporting goods, and medical implants. “These industries have incredibly precise specifications when it comes to their requirements – they use expensive and volatile elements such as nickel, chromium, niobium, and titanium which molecularly form the strongest metals, but also require controlled atmospheres when molten,” explains Lister. “The controlled atmosphere keeps the elements where they should be, in the metal, and not forming oxides and other non-desirable states of metal. Once the metal is chemically pure, Consarc furnaces refine the macro and microstructure to ensure that the metal ingots being produced are as homogenous as possible. These processes of chemical and structural uniformity are what allows airplane and aeroengine manufacturers to safely use their parts in highly demanding applications.”
The first Consarc specialty furnace was developed over 40 years ago, and, today, over half the vacuum, or controlled atmosphere melting furnaces around the globe bear the Consarc name. “Our name comes from our original product – a vacuum arc remelting furnace, or a consumable arc furnace, hence cons-arc,” says Lister. “Our core product offerings are VIM, which is Vacuum Induction Melting; VAR, which is Vacuum Arc Remelting; ESR, which is ElectroSlag Remelting; and VPIC, which is Vacuum Precision Investment Casting.
“Our typical customer is a specialty steel provider,” Lister continues. “It’s not the big name companies like U.S. Steel, Nucor, or ArcelorMittal. We work with a group of companies that most people haven’t heard of outside the industry. That includes companies like Carpenter Technologies, the Precision Castparts Group, Arconic, and Allegheny Technologies – you may not have heard of them, but they are all companies that are incredibly vital to the aerospace industry, keeping us safe when we fly.”
Consarc’s capabilities do not end with the design and manufacture of its products; the company also offers its customers the industry’s highest level of technical support and service based on its extensive experience in installation, repairs, and field service engineering. Additionally, in some industries, melting and refining involves more than just the equipment to perform the act – it requires the process knowledge developed over decades of experience. Consarc personnel around the world work directly with customers to refine their process, increasing production time, output, and repeatability.
Globally, Consarc has about 150 employees in many locations; it is headquartered in New Jersey with 4,200 square meters of manufacturing; operates an 1,800-square-meter manufacturing facility in Scotland, and partners with manufacturing teams at Inductotherm Group sister companies in China, India, Korea, and other countries.
This, Lister believes, is Consarc’s biggest advantage to its customers. “We have access to 40 different locations, globally,” he says. “We are on all six continents, so we’re able to provide local support in local time zones to our global client base. We can leverage the knowledge of 2,900-plus employees who have cumulatively been manufacturing for thousands of years and apply that knowledge directly to our local customers.”
This is particularly helpful in the steel industry, where gone are the days of a large team of plant engineers running a whole facility. “Today,” Lister explains, “we’re seeing jobs that were traditionally handled by the steel plants and their team of engineers being pushed on to the OEMs. Many of our clients are increasingly reliant on us for things like installation or process knowledge, and we’ve evolved accordingly. We have dedicated teams of installation specialists, as well as an extensive R&D department, with staff engineering and technical teams poised to handle our customer’s most intriguing challenges.”
Lister mentions some of the company’s signature projects and awards: “We did a project with Latrobe Specialty Steel, before their acquisition by Carpenter Technologies back in 2007-08. We delivered the largest vacuum induction melting furnace operating today while they were constructing their new plant. It was a collaborative design/build. While they were building, we were shipping components in and we are proud of what we did in a short span of time. That won an AIST (Association for Iron & Steel Technology) project award. We also manufactured a 150-ton static electrode ESR furnace which, when it was installed in 2011, was the largest of its kind.
Going forward, Consarc’s focus remains on leveraging today’s newest technologies for the benefit of its customers. Lister sees the future of Consarc intimately tied to the nascent industry of additive manufacturing, which refers to a process by which digital 3D design data are used to build up a component in layers by depositing material. “Additive Manufacturing (AM) is going to drastically change the way that engineers and end users are designing parts,” he states. “We’re seeing a tremendous upswing in research and development of high performance alloys for 3D printing. That means there is currently a tremendous demand for powders. There is no doubt this technology is in its infancy; we’re not going to be driving 3D printed cars anytime soon. But, we are seeing a lot of research and development and where there’s smoke, there’s eventually going to be fire.”
Meanwhile, Lister says that Consarc will continue to provide its full spectrum of services “to help companies with their equipment for its entire lifecycle – from pre-sales, to installation, to ongoing metallurgical support,” he concludes. “We’re making strategic investments into additive manufacturing, and supporting our customers in mature industries, like automotive and aerospace. We’re doing all that and keeping an eye on modernizing our product offerings for the future. We are an engineering company, striving to develop game-changing technologies, at heart; we just happen to also manufacture vacuum furnaces.”
Check out this handpicked feature on Innegra Technologies – High performance fiber.
AT A GLANCE
WHO: Consarc Corporation
WHAT: A leader in advanced vacuum technologies
WHERE: Rancocas, New Jersey
WEBSITE: Visit Site
PREFERRED VENDORS
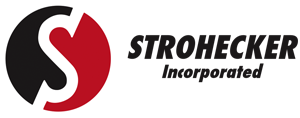
Strohecker Incorporated – Strohecker Incorporated specializes in the fabrication and repair of wrought copper crucibles, molds, liners, hearths, and related equipment for use in VAR, ESR, EBM, PAM and other related specialty melting processes.
Founded in 1947, Strohecker started as a custom fabricator of industrial equipment in high-temperature and corrosive environments. Soon after, Strohecker began developing techniques in the welding of heavy copper to itself and other dissimilar materials. It manufactured some of the earliest copper crucibles for the titanium industry and continued to develop its welding processes, so that by 1980, Strohecker’s crucible work had become the most important part of its business.
Situated midway between Pittsburgh, PA and Cleveland, OH, Strohecker draws from a wide range of experienced specialty forming, machining, heat treating and testing services – all within close proximity. For over 70 years Strohecker has provided quality fabrication and repair services to most of the specialty melting shops across North America, as well as to producers in Latin America, Europe, and Asia. – www.strohecker.com