AIM Aerospace, Inc.
Now it’s Sekisui Aerospace
Business View Magazine interviews Daniele Cagnatel, President & CEO of Sekisui Aerospace, for our focus on Domestic Manufacturing in the Composites Industry.
AIM Aerospace, Inc., based in Renton, Washington is a leader in the manufacture of advanced thermoplastics and intelligent automation for its customers in the aerospace sector, which includes such companies as Boeing, Kawasaki, Fuji Heavy Industries, Spirit AeroSystems, GE Aviation, Rockwell Collins, UTC Aerospace Systems, and Gulfstream, among others. The company provides closets, lavatories, overhead stowage bins, crew rest modules, seat furniture, flight deck doors, video control cabinets, sidewalls, storage products, cargo liners, structural composite assemblies, winglets, air handling system components, high temperature ducting, and environmental control system duct assemblies.
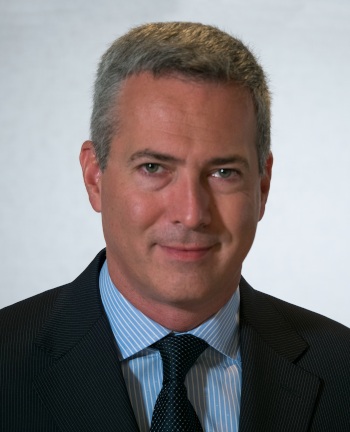
President & CEO, Daniele Cagnatel
While the company is 30 years old, over the last few years, AIM has experienced significant growth and change. In 2016, it was acquired by Liberty Hall Capital Partners, a private equity firm with interests in the aerospace and defense industries. With a mandate to grow the company’s capabilities and markets, the new owners quickly acquired Quatro Composites and its manufacturing facility in Orange City, Iowa, as well as its research center in Poway, California. Quatro brought a completely different capability to AIM, having developed a new type of carbon fiber technology in thermoplastics, using a unique process trademarked QFORGEM.
“They work with carbon fiber components which are more solid, stronger, and higher-tech primary and secondary structural components,” explains Daniele Cagnatel, President & CEO of AIM Aerospace. “They also work on unmanned aerial vehicles, and fuselages and wings for large commercial and military vehicles. One of the key reasons why QFORGE is so important is that it’s a fully-automated system, whereas the work we do in Washington State is very labor intensive. The system also incorporates the latest technology called ‘Industry 4.0.’ This technology has taken a strong foothold in Europe and has now become the buzz word in America, as well. Industry 4.0 is about connectivity; about automating a manufacturing system to create the repeatability process, and using data and data collection systems to get information out of the automation system and using that information to improve quality and productivity.”
“In our Iowa facility, we are able to monitor all the manufacturing processes and our scrap rate is absolutely minimal,” Cagnatel continues. “We deliver 5,000 parts per month to our customers using this technology with a perfect performance and no rejects. When you have the right information at your fingertips to monitor the manufacturing process, and it’s all automated, the level of value you can add is phenomenal. So, Quatro Composites was a great acquisition.”
The blending of the two companies allowed AIM to enlarge its product line, and this past year, Cagnatel reports that the newly expanded firm won several contracts to bring composite structure to jet engines. “We got to put carbon fiber components on the engine of the Boeing 777 and 787 aircrafts, and on the engine structures, also called nacelles, of the Airbus A350 engine,” he notes. (A nacelle is a housing, separate from the fuselage that holds engines, fuel, or equipment on an aircraft.) In the case of the 777 and the 787, we won contracts for carbon fiber components that were already being manufactured by the incumbent supplier, but we’ve been able, through our process technology, to provide a more compatible solution for our customer. In the case of the Airbus A350, the parts that we now provide for the nacelles used to be metallic, and we’ve been able to work with our customer to help them with the redesign of these metallic parts into carbon fiber and then, with a carbon fiber solution, it significantly reduced the weight of the structure. So, these will all be new planes built going forward; they are not retrofitted planes.”
“We’ve also grown our company by more than 100 employees, already this year,” Cagnatel adds. “Most importantly, though, we did hire an industry 4.0 team, and we put in place the first apps towards industry 4.0 digitalization, which, by the way, was directly linked to us winning those contracts for the jet engine components. While doing this, we have moved our research and development facility from California into our HQ in Renton, Washington, and moved the Industry 4.0 team, the automation team, as well as R&D for thermoplastic composites up here to be much closer to home and integrated with the rest of the team. We invested heavily in Washington; we completely refurbished one of our facilities where we make the environmental control system ducting for the Boeing aircraft, and we invested in automated machinery to help reduce all of the health and safety risks and to improve the utilization of our materials while reducing our impact on the environment.”
Perhaps the biggest, and most up-to-date, news for AIM was its recent acquisition by the Sekisui Chemical Company, Ltd., a ten-billion dollar company, based in Tokyo and Osaka, Japan for $510 million. Sekisui engages in the manufacture of high performance plastics for the medical, automotive, and information technology industries, as well as residential housing construction. Sekisui has nine facilities and offices spread across the U.S., but AIM will be its first on the West Coast. The buy of AIM is the largest acquisition ever made by Sekisui Chemical and will expand the company’s presence in the carbon fiber composites market and will increase sales of its thermoplastic resin materials for aircraft components.
“It’s a huge step forward for us,” says Cagnatel. “Sekisui has been in business for more than 70 years. They don’t do aerospace, so we are going to be their aerospace division and they’re going to use their financial power and industrial power to help us grow and prosper and become a much bigger company than we had any aspiration to become, before. And their vision is to create a company that manufactures and sells to the customer with zero impact on the environment. They have a very strong corporate social responsibility; they’re trying to create a company that improves the world for their children and their children’s children. This is a fundamentally different long-term view than what we had before. When you’re part of a private equity group, your strategy tends to be relatively short-term.”
“This is a company that wants to make sure that we stay stable; they don’t want to come in and change everything that we do,” Cagnatel adds. “It provides security for us, our customers, and our employees. They are very keen for us to think all the way to 2030, and to think about global expansion beyond the United States. They want us to look at doubling the size of our company both organically and acquisitionally, and they want us to expand our view of research and technology and become a more technologically-driven company while using their material expertise and research and integrating them into our space manufacturing processes. It will provide more value to our customers and we will be more competitive.”
It is anticipated that fusing technology related to composite materials, such as thermosetting and thermoplastic carbon fiber reinforced polymer (CFRP) held by AIM Aerospace, with resin compounding technology, fabrication technology, and technology related to thermoplastic CFRP held by the Sekisui Chemical Group, could promote the research and development of products that could contribute to improving safety and environmental performance while responding to increasing needs in the automobile industry, and toward the expansion of next-generation mobility such as flying cars and drones.
It appears that AIM is expecting space to become increasingly more crowded, going forward, and intends to be up for the task.
AT A GLANCE
Who: AIM Aerospace now Sekisui Aerospace
What: Designs and manufactures components for the aerospace industry
Where: Renton, Washington
Website: www.sekisuiaerospace.com