Newberry Tanks and Equipment
Strategic Expansion in Petroleum Equipment Manufacturing
Producing high-quality steel storage tanks that lead the market
Since its inception in 1927, Newberry Tanks and Equipment has exemplified resilience and growth in the dynamic realm of petroleum equipment manufacturing. From its origins as a modest provider of petroleum equipment, the company has evolved into a formidable force, recognized for producing high-quality steel storage tanks for the Petroleum and Oil -markets.
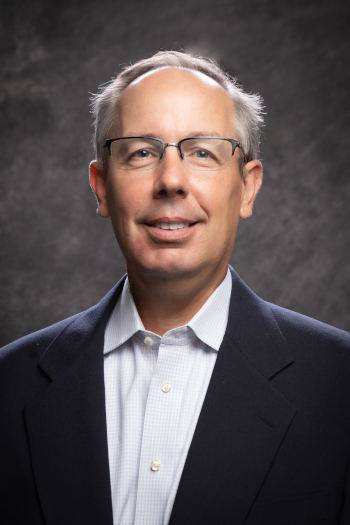
Matt Kohnke, President
Matt Kohnke, President and Chief of Operations, and James Fischer, Vice President, are at the helm of this enduring enterprise, deeply rooted in the company’s vision. With a history spanning three ownerships, Newberry Tanks and Equipment has found stability under the leadership of Chris Long, Chief Executive Officer, whose tenure commenced in 2010.
“Newberry has been through three ownerships in 100 years,” Fischer states. Since the acquisition in 2010, we’ve diversified our offerings to serve approximately 3,500 customers, spanning above-ground and underground storage tanks, including specialized solutions for the Automotive Oil Change Association.”
New strategies for expansion
Strategic milestones and expansions have punctuated the journey to prominence in the market. Fischer elaborates on the pivotal moments that have propelled Newberry Tanks and Equipment to its current stature, including the acquisition of Faith Tank, well-known for its expertise in manufacturing rectangular tanks for quick lube service centers.
“Our acquisition of Faith Tank marked a significant milestone in our expansion strategy,” Fischer notes. “Integrating their capabilities into our portfolio has fueled substantial growth, particularly in producing rectangular tanks.”
Newberry Tanks defies expectations with unprecedented growth in an industry projected to experience a revenue decline over the next half-decade. While the metal tank sector witnessed a significant 6% drop in revenue in 2023 alone, Newberry Tanks soared to new heights, with a 16% increase in revenue during the same period, following an impressive 36% surge the previous year.
An important point in the company’s evolution occurred in 2022 with the relocation to a larger, more efficient facility. This move not only doubled Newberry’s manufacturing capabilities but also tripled its production capacity for rectangular tanks, meeting the escalating demands of its clientele. The larger facility also allows Newberry to inventory and distribute the extra equipment needed by the lube industry.
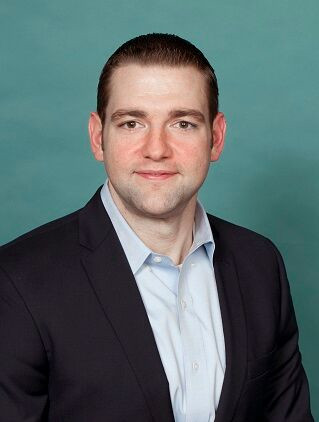
James Fischer, Vice President
“With our expanded footprint and increased work cells, we can now produce thousands more tanks annually,” Fischer explains. “This enhanced capability enables us to meet several large customer needs over the years ahead.”
People-first philosophy
Kohnke elaborates on the company’s recent achievements and initiatives to enhance operational efficiency and customer satisfaction. Among these accomplishments was the implementation of the Entrepreneurial Operating System (EOS) across all staff, a move designed to streamline processes and foster a culture of accountability and alignment.
“Our adoption of the EOS framework has been instrumental in driving organizational clarity and focus,” Kohnke explains. “By empowering every team member to understand our vision and execute their roles effectively, we’ve created a cohesive and agile workforce capable of navigating challenges and seizing opportunities.”
Implementing this system has yielded results, as Newberry has seen a 33% increase in its workforce since 2021. This influx of personnel highlights the company’s commitment to expanding operations to accommodate growing demand while maintaining exceptional standards of quality and service.
“The growth of our workforce reflects our dedication to fostering talent and investing in our people,” Kohnke emphasizes. “As we continue to expand our capabilities and offerings, our team remains our greatest asset, driving our success and propelling us toward our growth objectives.”
Streamlining operations with equipment kits
Another initiative driving Newberry’s growth trajectory is the Kitting Program. This strategic approach streamlines the procurement process by combining components or items required for a specific task or project.
For Newberry Tanks and Equipment, kitting refers to assembling all the necessary equipment and accessories that accompany a steel tank into convenient kits. This includes lubrication equipment, fluid systems, pumps, valves, and vents. Packaging these components together ensures that customers have everything they need for their operations in one comprehensive package.
This simplifies the purchasing process and enhances efficiency and convenience for customers, as they no longer need to source these items from multiple suppliers. Ultimately, kitting enables Newberry Tanks to provide a seamless, one-stop solution for their customer’s needs in the petroleum equipment manufacturing industry.
“By consolidating their sourcing to a single supplier, we not only simplify their operations but also deliver cost efficiencies and operational synergies, positioning Newberry as a trusted partner in their success,” Kohnke notes.
Newberry’s partnership with Balcrank Corporation as a supplier of oil and lubrication equipment for Newberry’s kitting program is another prime example of mutual growth. This partnership has propelled Newberry from being a top-10 regional distributor of Balcrank products to claiming the number-one spot nationwide, highlighting the synergy between the two entities.
Navigating an evolving landscape
For the fifth consecutive year, winning the Company of the Year title in metals and mining, at the American Business Awards, Newberry Tanks and Equipment has faced numerous challenges in navigating the turbulent manufacturing industry landscape. One prominent obstacle has been the scarcity of skilled labor, particularly evident during the tight 2022 and early 2023 labor market. Kohnke sheds light on the company’s strategy for addressing this issue, stressing implementing a pay-for-production system that grants welders autonomy over their earnings, incentivizing efficiency while maintaining quality standards.
“Our unique pay-for-production system gives welders the autonomy to determine their earnings,” Kohnke explains. “By aligning incentives with productivity, we’ve been able to attract and retain skilled labor, ensuring a steady workforce capable of meeting the demands of our expanding operations.”
Fischer elaborates on additional challenges, including the delicate balance of pacing growth to synchronize with manufacturing capabilities and market demand. Like many companies, Newberry faced the challenge of managing fluctuations in the steel market, necessitating agile strategies to mitigate the impact of price volatility on production costs and customer relations.
“In times of uncertainty, such as during the COVID-19 pandemic, maintaining steady revenue growth while navigating market fluctuations becomes paramount,” Fischer remarks. “Our ability to adapt and invest in production capabilities has allowed us to address these challenges effectively, ensuring minimal disruption to our operations and timely delivery to our customers.”
The customer experience
Its customer-centric practices and continuous improvement are central to Newberry’s resilience amidst industry upheavals. Kohnke highlights the company’s transformative approach to lead time management, shifting from traditional industry norms to a proactive stance focused on meeting customer deadlines.
“We’ve redefined the customer experience by prioritizing delivery timelines over lead times; through streamlined processes and enhanced communication, we give our customers unprecedented visibility into the production journey, ensuring they receive their orders precisely when needed.”
One such initiative is Newberry’s three-call process, which fosters transparency and accountability throughout the order fulfillment cycle. This approach involves regular communication with customers at key stages, from order confirmation to production scheduling, offering real-time insights into the status of their orders.
“By keeping customers informed and engaged throughout the production process, we not only enhance order accuracy but also cultivate trust and loyalty, distinguishing Newberry as a leader in customer service within the industry,” says Fischer.
In response to customer demand, Newberry Tanks expanded its e-commerce capabilities, boosting sales by attracting new accounts with substantial growth potential. One customer, initially acquired through the online portal, had never purchased a tank from Newberry Tanks before 2022. However, by the end of 2023, this customer had amassed an impressive $200,000 in orders, showcasing the effectiveness of the company’s enhanced online presence.
Newberry’s vision for growth
As Newberry Tanks and Equipment continues its growth trajectory, the dedication to overcoming challenges and exceeding customer expectations remains the cornerstone of its success. With a steadfast focus on quality, efficiency, and customer service, the company stands prepared to navigate future obstacles and solidify its position as a leader in the petroleum equipment manufacturing landscape.
“Newberry’s success is rooted in our steadfast dedication to excellence and innovation,” Kohnke affirms. “Through the EOS framework, we prioritize clarity, accountability, and collaboration, enabling us to navigate challenges and seize opportunities with agility and purpose.”
“As we look ahead to 2024, our focus remains on driving sustainable growth and operational excellence,” Fischer states. “By investing in infrastructure and technology, streamlining processes, and fostering a culture of continuous improvement, we expect to continue to grow the business, both the top and bottom line.”
AT A GLANCE
Newberry Tanks and Equipment
What: A leading fabricator specializing in steel storage tanks for the petroleum and gas sector in the nation.
Where: West Memphis, Arkansas
Website: https://newberrytanks.com/
PREFERRED VENDORS
Krueger Sentry Gauge Krueger Sentry Gauge – www.ksentry.com
With 80+ years of experience, Krueger Sentry Gauge has manufactured over 3 million level gauges. With a simple mechanical design, our sight gauges provide durability, simple repairs, and easy installation. Our tank monitors are available in many materials from galvanized steel, stainless steel, PEEK, PVC, and Kynar plastics. And all of our products are manufactured in the USA.