A world-class leader in roof racks and cargo management systems
Decades ago, if you wanted to take some extra luggage or other bulky items along on a car trip, you only had a few choices in terms of the type of cargo roof rack you could utilize. Some ancient models were made of wooden slats attached to a steel frame; others were simply a couple of cross bars fastened to the car roof by suction cups, or a combination of straps and clips. But even a quick look at today’s automobiles, trucks, and SUVs would reveal a veritable revolution in the design and application of the modern roof rack, showing just how far this value-added, automotive accessory has evolved over the last several years.
Today, roof racks and automotive racking systems are technologically complex, innovative in their fabrication and production, and according to Jeff Cavalier, Engineering Manager for JAC products, one of the top five aesthetic considerations that new SUV buyers list as important when looking for their next vehicle purchase. No longer a clunky afterthought, the modern roof rack is “a piece of jewelry on that roof,” says Cavalier.
JAC Products, Inc. was founded in 1967, and today is a leading designer and manufacturer of automotive roof racks and cargo management systems, supplying the world’s top car manufacturers. Its customers include: Ford, Toyota, Honda, General Motors, Subaru, Renault, Hyundai, Chrysler, Kia Motors, Nissan, and Peugeot. With offices around the world and manufacturing facilities in Michigan, Georgia, and Portugal, JAC is a pacesetter with extruded aluminum designs. JAC’s engineering and manufacturing capabilities also include plastic injection molding and steel rollform for the base components.
Cavalier is part of the manufacturing staff in JAC’s Franklin, Georgia facility, which was set up as an aluminum extrusion plant in the mid-1960s, and was taken over by JAC 20 years ago to help the company supply its aluminum-based products to the automotive industry. The extrusion lines produce millions of pounds per year of the 6XXX series aluminum for their product.
But with only about 1500 employees in North America, JAC is far from the biggest player in the game. Its competitors include the WKW Automotive Group, headquartered in Germany; DURA Automotive, with more than 21,000 employees in 15 countries; and the MINTH Group from China, whose customers represent 80 percent of the total global auto market share. “If you look at the size of us compared to those companies, we are relatively small,” Cavalier admits.
“What we do better is turn our product around for any kind of engineering, and I think we give a better product due to the type of technologies that we have. It’s not just taking metal and doing CNC (Computer Numerical Control) work or cutting it to a certain length. We have to stretch form it to fit the profile of the roof line of the vehicle.” Cavalier maintains that creating the perfect roof rack is not the typical X-Y arrangement. The shaping of the rail, and forming it, can be complex: “The stack-up and tolerances of the rail arrangement is defined by tenths and hundredths of a millimeter. That is something that makes us stand out above the rest.”
Cavalier continues: “Manufacturing practices are challenged on every program by multiple areas of responsibilities. The effect of deliverables for our product is very important. From the manufacturing process being repeatable to the support from the material management group, we have to be effective to support the production areas. Customer satisfaction is our business. Production units do that with a quality part delivered on time. From new products to continuous improvement activities, we push to be better for our customers.”
JAC’s Cargo Management Systems for the trucking industry include side rails, header bars, bed dividers, load bars, lockable storage bins, and other storage options. “Some of our innovations with racking systems for work trucks, I think are top-notch and world-class,” says Cavalier. “We’re proud of that and we’re going to see more of those types of innovations we put out for cargo management systems. We’re broadening our expertise on how to do complex step rails. Our customers are giving us opportunities and all we can ask for are opportunities. And if we perform well, then we can maintain a strong business at that point.”
In addition to its roof rack business, JAC Products also supports the aluminum substructure within the automotive industry, as the auto companies continue to make the switch from steel to aluminum in order to make cars lighter. That often requires JAC to make certain changes to the aluminum alloys that it provides to the car manufacturers since they are also moving rapidly to the robotic welding of parts, rather than bolting them together. It’s another reason why the company’s development group in Michigan stays closely involved with the car manufacturers’ engineers.
“I’ve got to give credit to Product Development,” says Cavalier. “They’re constantly trying to understand the movement of what the market’s going to be two years and five years and ten years out, and what the customer thinks – that keeps us in the conversation. It’s just a matter of how much business we can develop with our relationships. We want to make sure that we’re one of the key players within the OEM process; that we have more capabilities than just roof racks.”
In order to keep on the cutting edge, JAC’s technology is also reaching into areas like cameras and LED lighting systems that can be incorporated into the roof racks, themselves. “We can put cameras in a roof rack to get a 360 view around any vehicle. We can put security systems in a roof rack. It’s not just about metal working; it’s about the whole technical field and how it’s integrated into the car and what it means to safety and to the vehicle’s appearance. We want JAC to truly be involved in anything that’s going to be innovative in that vehicle because we have the capability of doing that.” In addition, the coatings and sealings of JAC’s products have to stand up to years of harsh car wash detergents and rough weather, so the company does a lot of testing of its various finishes.
Cavalier also admits that proximity to the manufacturers, both in Michigan and the southeast, where more auto plants are being built, is helpful. “Franklin is in a good location for us to meet delivery needs. Any time we can minimize the amount of freight that just helps the cost to our customers.
As Cavalier looks ahead, he sees JAC Products maintaining its strength in the things that it does very well, but also expanding its territorial spread and product lines. “When you think roof rack, you ought to be able to think JAC Products. But the biggest thing is to make sure that we grow in a diversity of products that we give our customers, particularly the OEM, and maintaining those relationships, not just in North America, but world-wide. The auto industry in China is very big and being able to be part of that over there would be huge for JAC; the same in Central and South America. There are arenas that we haven’t tapped into and we want to. Let’s go into other markets in things that we do very well. Then let’s also diversify our product line to show that we’re more than roof racks. If we can grow that capability, that would be a huge thing for JAC Products.”
JAC Products may not be the world’s biggest roof rack and cargo management company out there. But with its innovative technologies, coupled with a fierce desire to satisfy its customers’ demands, it certainly is on top in North America – and in the near future, it expects to be on top on other continents, as well.
AT A GLANCE
WHO: JAC Products Inc.
WHAT: Manufacturer of roof racks and cargo management systems
WHERE: Saline, Michigan
WEBSITE: www.jacproducts.com
PREFERRED VENDORS
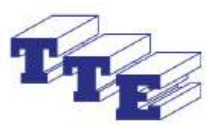
Thumb Tool & Engineering – Thumb Tool & Engineering is an aluminum extrusion die company. It was acquired in 1998 by the metals division of the Gemini Group, a financially diverse firm with holdings in manufacturing, banking, real estate, land development, and energy. In 2013, Thumb Tool & Engineering joined forces with Mid-South Extrusion Die and Central Extrusion Die and, in doing so, positioned Gemini Group as the second largest supplier of aluminum extrusion dies and tooling in North America. The company’s engineering department uses CAD-CAM programming to ensure its customers exact geometry when designing their profiles. Its drafting team has an impeccable reputation as effective communicators who listen to their customers’ needs and fulfill their requirements. Along with the latest technology in design and manufacture, Thumb Tool & Engineering offers over thirty years of experience in the die making industry. Its reputation was built on the highest quality tooling, fast deliveries, and competitive prices. – www.geminigroup.net