A&C
Your global GMP partner
Business View Magazine interviews Ken McCracken, President and CEO of A&C, for our focus on the
Biotech Life Sciences Industry
By definition, GMP (Good Manufacturing Practice) is a system for ensuring that products are consistently produced and controlled according to quality standards. It is designed to minimize the risks involved in any pharmaceutical production that cannot be eliminated through testing the final product. That designation is never to be taken lightly, as A&C knows full well – being a leading global GMP manufacturer of excipients, buffers, process solutions, and a select number of active pharmaceutical ingredients (APIs).
A&C has been servicing the life science industry since 1966, and expanded its footprint through the years to now having offices and GMP production facilities in North America and Europe. The privately-owned, service-driven company excels at finding unique solutions to its customers’ GMP challenges; placing transparency, quality, and the ability to adapt at the core of its activities. Since March 2020, A&C has been developing GMP raw materials and buffers for major clients in their pursuit for a vaccine for SARS-CoV-2 (COVID-19). A&C’s flexibility and responsiveness have allowed for the fast development and delivery of these raw materials to customers, enabling them to move swiftly with vaccine development.
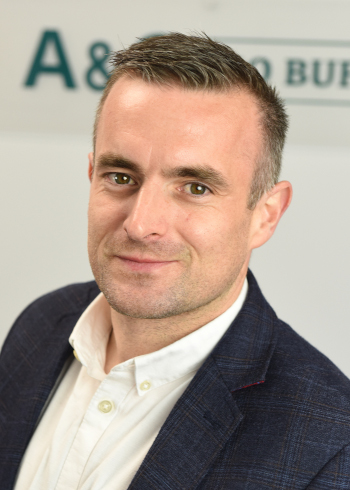
Sales & Marketing Director, Gearoid O’Rourke
Business View recently spoke with A&C President and CEO, Ken McCracken; Sales & Marketing Director, Gearoid O’Rourke; and VP of Business Development, Luc Miron about their revolutionary company and the vital services it is performing for the global good. The following is an edited version of our conversation.
BVM: Can you describe the beginnings and evolution of A&C?
Ken McCracken: “A&C was founded by two individuals who had been working for a major pharmaceutical company here in Montreal for several years. They were developing different products and services within the company that they felt could possibly serve the industry as a whole. Consequently they decided to venture out, put up their own shingle, and started selling into the industry from a garage. They began developing and manufacturing different lab chemicals and reagents and, as the business grew, a lot of those products became ingredients within different products. The company also evolved with its quality systems along the way to support that. When Luc and I acquired the business in 2003, it was a company with potential that the existing ownership had wanted to keep at a manageable size.
“We saw the diamond in the rough and decided to focus our business on expanding the services we can offer our customer base in the pharmaceutical sector. Subsequent to that, we recognized a need based on demands by our customers to meet their requirements, not only here in Canada, but on an international scale. So we established a U.S. entity, as well as an entity in Ireland to service the needs of Europe. Since then, we’ve gained a considerable amount of traction within the overall pharmaceutical market with many of the major players. Being able to service their needs on a global basis has helped us position ourselves well within the marketplace.”
BVM: What do your operations entail?
O’Rourke: “We have two manufacturing plants in the Greater Montreal region – Site A in Montreal that has been in operation over 50 years, and Site B in Baie-D’Urfé that opened about four years ago. Our third facility is located in Limerick, Ireland and opened about two years ago. They are all ISO certified and Site A, our main facility, holds a Drug Establishment License for the manufacture of APIs, and an EXCiPACT certification for GMP and GDP. We also have 30 customer audits at the facility, and we are FDA and Health Canada audited, as well.
“The Irish facility is predominately set up for the manufacture of buffers, process solutions and chemical blends for the pharmaceutical industry. We’ve recently worked on a number of projects related to COVID-19. Site A in Canada is APIs and excipients, and Site B is predominately all excipients, and a number of raw materials. We also have some legacy business which is specialty chemicals – that division was set up 50 years ago and the business still thrives out of Site A in Montreal.”
BVM: How has COVID-19 impacted your business?
O’Rourke: “One of our target markets for the last few years has been in the biotech, biopharma, and injectable sectors and we’ve been supplying a number of world leaders in vaccines for more than 10 years. We were approached by one large German vaccine developer at the start of COVID; they asked at our Irish facility if we would get involved in the manufacture of three new raw materials required for the manufacture of the vaccine. It was all hands on deck and our Canadian facility staff and our Irish facility worked in tandem, nights and weekends, to meet the aggressive deadlines. Thankfully, we were able to do so, which allowed that vaccine to move forward into human clinical trials. It is now in Phase III and showing positive results. We’ve also worked on a couple smaller CSR projects, where we provided raw materials for ingredients in hand sanitizers, and we actually manufactured hand sanitizer out of Europe, as well, and gave it to some charitable organizations.”
McCracken: “Obviously, at the beginning of the pandemic our concern was on our employees, as well as ensuring that we continued as an essential service business. We looked at the different products we sell to ensure that those which would be required to service our customers’ needs were prioritized. We immediately took action and were proactive throughout the entire process. Well ahead of receiving any external directives, we took charge ourselves to ensure the continuity and security of supply.
“Beyond that, there were some community activities. We donated materials to a Montreal firm that was manufacturing hand sanitizer for the community and helped work on the formulation to make sure it was done in a safe and secure manner. We did receive a lot of phone calls early on for additional business but that was not our main concern. We decided to be grounded in terms of existing supply and I think that bodes well, because most of our business is long term with the current priority being the vaccine manufacturers.”
BVM: What role does company culture play?
Miron: “The true heroes have definitely been our employees during COVID. There was so much uncertainty and yet they came to work and kept the supply chain going for our customers. It was tough times and they did an amazing job. Our employees have been with us over 15 years, on average. We have one at almost 40 years and a few at 30, but they are all great.”
McCracken: “Coming to work in this field and playing the role we play is very motivating. It’s part of the company culture and I believe it’s reflected in our employees. Without their talent and the effort they put in on a daily basis, we would not be where we are today. And it’s done collectively, whether in Ireland, or the U.S., or Canada, we operate in a global manner as a team.”
O’Rourke: “When Ken and Luc took over the business, they identified a need within the pharma and the biopharma industry for suppliers that really understood the GMP requirements of the drug manufacturers. On our side, we felt that we needed to go a step further. We wanted our team to become part of our customer’s team. And we wanted each department in our organization to have direct contact with our clients so they could work in unison to solve problems in a quick and responsive manner. So we developed the Partner Service Organization (PSO) approach that now runs throughout our business to find unique solutions to our customers’ GMP challenges.”
BVM: What are the biggest challenges facing A&C?
McCracken: “We’re continually looking for efficiencies – a lot of what we do is customization to meet customers’ needs. Striking the right balance of having efficiencies where it makes sense to the industry itself. There is a lot of demand for it and we need to remain agile as we continue to grow our business.”
O’Rourke: “COVID has changed how we interact with clients. Because it’s highly customized, usually there would be a lot of face-to-face meetings and dialogue amongst our teams. That’s completely changed. We communicate via video conferencing and we use a project management software which allows our customers real-time access and data to follow our projects. Everyone is adapting and learning – our team has embraced it and our customers have as well.”
BVM: Looking ahead, what are the main objectives for A&C?
O’Rourke: “We’re in the middle of a strategic planning process, identifying goals for the team and the group. They include continued growth and expanding our footprint into different regions. We’ve a very strong and vibrant culture within our team, and embedding the new staff into that positive culture and the PSO approach is very important.”
Miron: “We will continue our selling position, making sure we support our customers and see where we can expand to other projects with the facilities we have.”
McCracken: “The market will dictate to a certain degree and we will put our best foot forward and position ourselves. But we definitely want to be our customers’ preferred service provider of custom GMP ingredients and process solutions for the global life science industry. We can’t be everything to everyone and we have to focus those efforts with the right industry partners and provide them with our services.”
Pictured at top from left to right: Damien O’Rourke (VP and COO), Ken McCracken (President and CEO), Luc Miron (VP Business Development), Peter McGarry (CSO) and Jean-François Raymond (Quality Director)
AT A GLANCE
A&C
What: Leading GMP manufacturer for the global life sciences industry
Where: Head office in Montreal, Quebec
Website: www.acggp.com www.acbiobuffer.com (Ireland)
PREFERRED VENDORS
VAC-U-MAX www.vac-u-max.com
VAC-U-MAX is a worldwide leader in the design and manufacture of powder and bulk material handling systems that incorporate pneumatic, aero-mechanical and flexible screw conveying technologies. Since 1954, VAC-U-MAX has defined leadership in bulk material handling, designing, and manufacturing systems that handle over 10,000 various powders and granular bulk materials for process industries worldwide. With manufacturing and test lab located in Belleville, New Jersey, VAC-U-MAX equipment, and solutions have worldwide representation through manufactures representatives throughout the world. Product range includes pre-engineered and custom vacuum conveyors for general purpose and sanitary applications, bulk bag loading/unloading systems, bag dump stations with integrated LoadLifter™ bag lifting system, batch-weighing systems, multi-ingredient handling systems, mobile conveying systems, feeder refill systems, and aero-mechanical / flexible screw conveying systems. Product range also includes a full line of industrial vacuum cleaners, including compressed-air operated vacuum cleaners for combustible dust, flammable liquids, and reactive powders. For more information or to discuss your application with our bulk material handling specialists, visit www.vac-u-max.com and fill out request-for-quote.