FirstStar Recycling
For the sake of the planet
Business View Magazine interviews Dale Gubbels, CEO of Firststar Fiber, Inc., for our series on Strength and Growth in the North American Recycling Industry.
For 22 years, FirstStar Fiber, Inc., operating as FirstStar Recycling, has been doing its innovative best to help save our planet, and that passion is getting stronger and more creative all the time. The firm was formed in 1997 with the mission to enhance Nebraska’s recycling infrastructure. Operations began in the spring of 1998 in Fremont, and relocated a year later to a larger Material Recovery Facility (MRF) in Omaha, nearer the company’s growing customer base. Today, First Star Recycling employs over 130 people at its sites in Omaha and Lincoln, Nebraska, where it processes recyclables for businesses and communities throughout the Midwest, and markets close to 100,000 tons annually to end users throughout the country and internationally. First Star’s mechanical sorting process was the first of its kind in Nebraska and is still the largest in the state, providing commercial and residential customers the most convenient and comprehensive means to recycle.
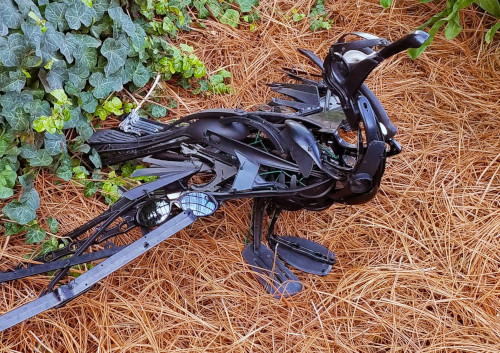
Lauritzen Gardens
Dale Gubbels, CEO of FirstStar Fiber, Inc., explains, “FirstStar Fiber, Inc. is our corporate entity. The reason for having ‘Fiber’ in the name is because we started the company with the idea of building a paper mill, but that didn’t pan out. So, we do business as FirstStar Recycling to make it clear what we actually do. Our initial focus was solely on paper, but we’ve grown to encompass a wide variety of materials from residential and commercial sources.” FirstStar doesn’t participate in the curbside pickup of regular residential recycling – they leave that service to municipalities or haulers. For commercial businesses, they arrange to have company-owned semi-trailers park at the customer’s dock, where they are loaded with recyclables and then trucked back to the plant for processing in either Omaha or Lincoln.
“We don’t turn the recycling into finished products,” Gubbels notes. “We sort the materials, using quality control methods to ensure when we ship them out to end markets that they’re getting the commodity they need for their operations. For example, residential recycling is put out to the curb by the homeowner, or taken to drop-off locations, in a co-mingled fashion and we have to separate those materials into their respective commodity types: newspaper, cardboard, aluminum cans, plastic, and so on. Then it’s our responsibility to find consumers, or end markets, who turn them back into a variety of products.”
While shipments are made to export markets in South Korea, Malaysia, India, China, and Mexico, the majority of material stays stateside. The company signed a long-term contract with the City of Omaha in 2015 to process their recyclables through 2020, with automatic opportunities for renewals for a total of 20 years. Due to the large outlay of capital needed for specialized mechanical sorting equipment, FirstStar Recycling is the only MRF in Omaha. Competition comes from two similar, yet smaller, companies and , but First Star’s system for material processing is much more sophisticated. They pull in material from a wide region, that includes the city of Omaha and the metropolitan area, Kansas, Missouri, Iowa, even as far away as and Wyoming.
Dow Chemicals started the Hefty Energy Bag program in California as a pilot, and FirstStar was the first MRF in the country to permanently add the program to its offering. They’ve now been doing it for over two years. Residents buy the bright orange, 8-gallon bags and fill them with, otherwise, non-recyclable plastics, such as potato chips bags, straws, candy wrappers, and film of all types. The Hefty energy bags are set out to the curb with recyclables, where they are retrieved and the contents sent to a pyrolysis plant. There, the materials are heated up in the absence of oxygen and converted into diesel; keeping those plastics out of the landfill and turned into a usable resource. Gubbels reports, “One of the reasons we’re anxious to do more with the Hefty Energy Bag program, is we see it as a great opportunity for a lot of businesses, such as pyrolysis companies, and cement kilns, that can use this material. It’s also perfect for communities and businesses that want to divert more material from their landfills to adopt this as a program. So, we’re working with our partners: Reynolds, that manufactures the energy bags; and Dow, that first came up with the concept for the program, to expand it throughout the U.S. and into Canada.”
Studies have shown that using recycled materials, as opposed to virgin commodities, in any manufacturing process that needs, for instance, aluminum or plastic, results in energy savings. And there’s a growing sentiment around the world that, because the earth has limited resources, we can’t continue to employ the linear concept of “use it, abuse it, and throw it away.” The circular economy is what many environmentalists and economists are touting to ensure economic sustainability. That being said, one of the biggest challenges in the recycling industry is the need for more markets.
“We employ one person whose sole job is to go to trade shows and search web pages to find the markets that need recycled material,” says Gubbels. “Our customer base is a two-prong system. We have customers who are in need of materials, and then we have to go out and find those materials. That requires us knocking on doors, going to trade groups, networking here in the Greater Omaha area and in Lincoln. We also do a lot of brokerage type work; meaning that once we make arrangements with a mill or end market that wants this material, we can also reach out to businesses who are producing quantities of material as bi-products and arrange for them to get a baler or other means to process their discards and send it directly to the end markets. The material never comes to us. We’d like to expand in that area in the future.”
In the technology realm, FirstStar recently installed two optical sorters which have the capability of identifying everything that comes down the conveyor. The first has a program to pull off water and soda bottles, and anything made of PET polyethylene terephthalate; and the second is programmed to take out milk bottles, shampoo bottles, laundry detergent bottles, and anything made of HDPE high density polyethylene. These two optical sorters do a lot of the work that used to be done by hand. “We were actually one of the first MRFs in the country to trial the use of a robot,” says Gubbels, “In fact, we were so early on with it, the company Amp Robotics, out of Colorado, had just started developing the system and they were very grateful of the work we put in to help them figure out how to do it. With our new container line, we’re talking to them again – now that they’ve greatly perfected their initial version, we’re looking at the possibility of installing several robots in the near future.”
Community involvement is an important part of the FirstStar culture, and the company avidly supports Keep Omaha Beautiful and Keep Nebraska Beautiful. It is also a member of the Association of Plastic Recyclers, the Nebraska Recycling Council, and the Business Ethics Alliance, which is based in Omaha. That organization’s mission is to help companies navigate ethical questions about business, and is a partnership among regional businesses, Creighton University and other local colleges, the Omaha Chamber of Commerce, and the Omaha Better Business Bureau.
Looking ahead, FirstStar Recycling has some ambitious objectives. “We’re looking at ways we can establish end markets closer to us,” says Gubbels. That includes putting a pyrolysis system in our own facility that would enable us, rather than shipping off unrecyclable plastics, to process the material and return it to diesel right on our site. And the City of Omaha is in the process of changing its residential recycling system from small, open 18-gallon bins to 96-gallon carts. So, one of our future needs will be to expand our processing capability because wherever communities have made that kind of change, they’ve seen tremendous growth. Just this past spring, the nearby City of Bellevue has switched to carts and we’ve seen a doubling of the recycling their residents have started to recover. Bellevue is on a weekly schedule but Omaha will have recycling pickup every two weeks, like some other communities in the area, to save money.”
In summing up the most important attributes of FirstStar Recycling, Gubbels shares, “The major thing that separates us from many material recovery facilities is we’ve always been very innovative; sometimes by necessity, because we’re a long way from end markets, but we’ve also recognized the fact that we have customers on both ends of our business – the suppliers as well as the end markets. Our challenge, and our strength, is recognizing that both of them have to be treated well in order for the materials that flow between the two to actually be successful.”
Check out this handpicked feature on Institute of Scrap Recycling Industries.
AT A GLANCE
Who: FirstStar Fiber and FirstStar Recycling
What: Recycled material recovery company
Where: Omaha and Lincoln, Nebraska
Website: www.firststarrecycling.com